Revolutionizing the Foam Sector with the Power of the Digital Twin
UREBLOCK, one of the leading manufacturers of polyurethane foams, faced the challenge of expanding their facilities. The increasing demand for their products required expansion, but how could they assess the feasibility of this decision without incurring significant financial and operational costs from the outset?
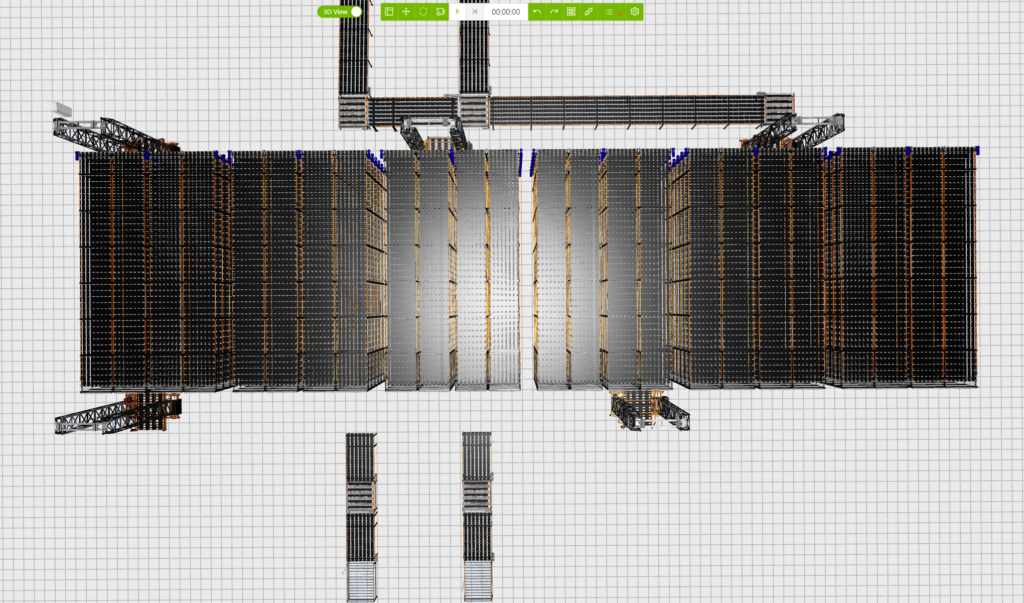
The solution came with SIMUMATIK’s digital twin. In collaboration with IPF, UREBLOCK used this innovative platform to virtually explore the expansion of their plant without moving a single nut or bolt.
Here are the key points that outlined their development:
Optimization of Production Processes
The digital twin allowed UREBLOCK to meticulously analyze every aspect of their in-plant logistics operations. This gave them the opportunity to identify potential bottlenecks, optimize workflow, and design a plant layout that maximized efficiency and productivity.
For SAS, it was used as a means to verify that all automation aspects worked correctly and to anticipate potential issues during commissioning. Additionally, it opened a door to innovation in automation, creating a high-performance factory.
How was it done?
Through OMRON brand PLCs, specifically the NX and NJ series in coordination with Sysmac Studio software and the SIMUMATIK platform. SAS made the necessary modifications according to new production standards. Below, you can find a video showing how these three elements interact in practice:
One of the strengths of this digital twin is its ability to replicate potential production processes without moving a single nut in the factory, simply by preloading these adjustments into the PLC.
Comprehensive Plant Vision
Thanks to SIMUMATIK’s digital twin and the collaboration with IPF, UREBLOCK was able to advance their expansion project with confidence, knowing they were making well-founded and profitable decisions for the future of their company.
This allowed them to optimize their expansion plan, minimizing costs associated with design errors, delays, and last-minute changes, thus ensuring a profitable investment.
Conclusion
The digital twin confirmed that the feasibility studies were correct, verified the plant layout, and studied possible interactions with the automation part. This opened up the opportunity for our client to have a high-performance factory with high levels of efficiency, improving the key KPIs of their production process.