Revolutionizing Garment Decoration and Harnessing the Power of Virtual Testing
Kornit Digital, a leader in textile production tech, took a leap into virtual testing to enhance their development workflow for a new innovative garment decoration solution, the Apollo Platform. By creating a Digital Twin of their machine, they could try out different scenarios, identify anomalies, and make improvements to keep downtime to a minimum, all in a virtual space.
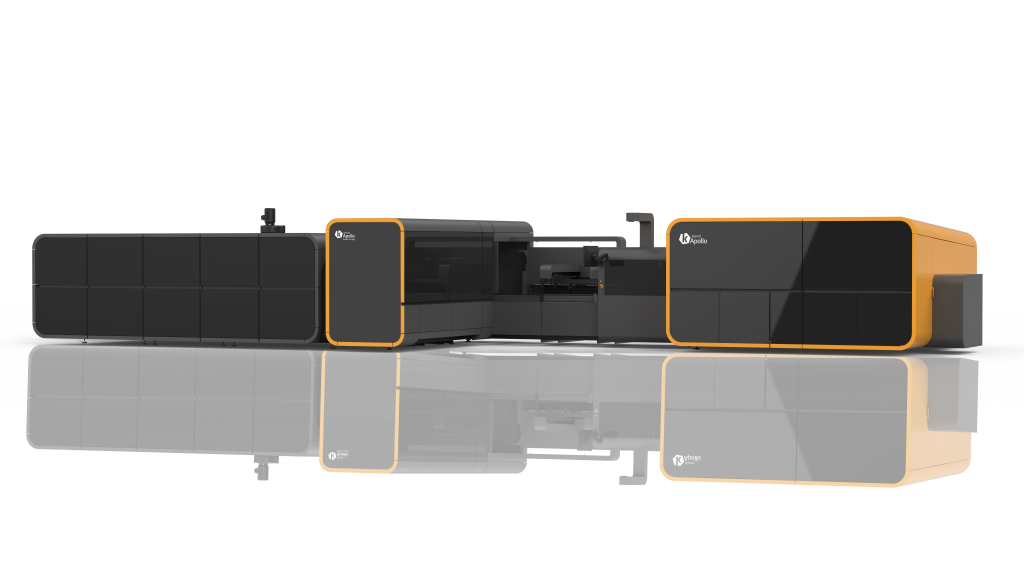
Leading the Way: Kornit Digital’s Sustainable Innovations in Textile Technology
Kornit Digital is a leading manufacturer of direct-to-garment and direct-to-fabric printing technologies for the textile industry. Their systems have been widely recognized for their innovative concepts and have significantly improved the sustainability of the textile industry by minimizing waste and water consumption.
When they set out to create the Apollo Platform, a machine made to decorate 400 unique garments per hour, extensive testing of its IT and OT systems was crucial. So, they turned to virtual testing to ensure smooth operation.
Testing the Apollo Platform: Navigating Complexity and Innovation
Simplifying Testing: Testing the Apollo Platform’s complex systems was no small feat. They needed a way to simulate real-world scenarios without the hassle of physical prototypes.
Software Complexity: Understanding how all the software components interacted and ensuring their proper functioning was challenging, being thorough was necessary to ensure everything operated smoothly as intended.
Handling Scalability: Testing the Apollo Platform’s ability to scale up production efficiently to meet increasing demand.
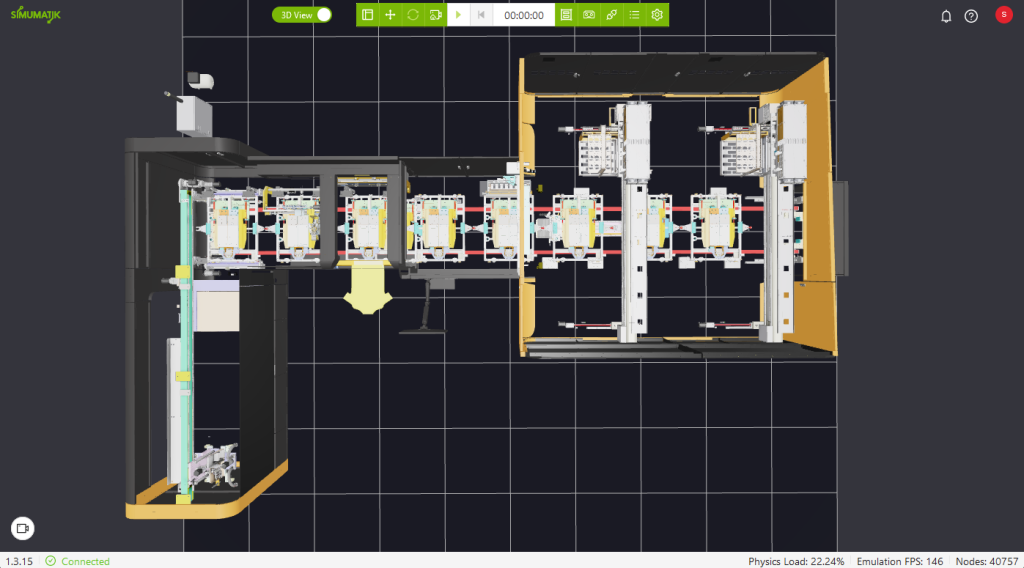
Strategic Decision-Making: The Choice of Virtual Testing for Innovation and Efficiency
Efficiency and Cost Savings: Virtual testing offered a streamlined approach, saving valuable time and resources by eliminating the need for physical prototypes.
Thorough Testing in a Virtual Environment: By creating a Digital Twin of the Apollo Platform, Kornit Digital could conduct comprehensive testing in a simulated setting, ensuring thorough evaluation of the system’s performance.
Alignment with Innovation and Sustainability Goals: Embracing virtual testing was in line with Kornit Digital’s commitment to innovation and sustainability, reflecting their forward-thinking approach to technology development.
Optimizing Performance: Achieving Excellence Through Virtual Testing
Kornit Digital teamed up with Simumatik to create a Digital Twin of the Apollo Platform. This helped them test and tweak the machine during development, saving time and boosting efficiency.
Speedy Development: Virtual testing helped Kornit Digital catch and fix issues early on, speeding up the development process.
Better Performance: Using the Digital Twin, the engineers at Kornit fine-tuned the Apollo Platform for peak performance, cutting downtime.
Cost Savings: Virtual testing reduced maintenance costs and made operations smoother, saving money in the long run.
Embracing the Potential of Digital Twins: Driving Innovation and Efficiency
Through virtual testing and the creation of a Digital Twin for the Apollo Platform, Kornit Digital achieved significant advancements in innovation and operational efficiency. By simulating real-world scenarios, Kornit Digital optimized performance, minimized risks, and delivered cutting-edge solutions to customers.
The integration of Digital Twins streamlined testing procedures and accelerated development timelines, fostering a more agile and responsive approach. Moreover, by reducing reliance on physical prototypes and minimizing environmental impact, Kornit Digital reinforced its commitment to sustainability.
In summary, the adoption of Digital Twins has revolutionized Kornit Digital’s approach, ensuring optimal functionality and reliability. As Kornit Digital continues its journey, the integration of Digital Twins will remain pivotal in shaping a more efficient, sustainable, and innovative future for textile production.
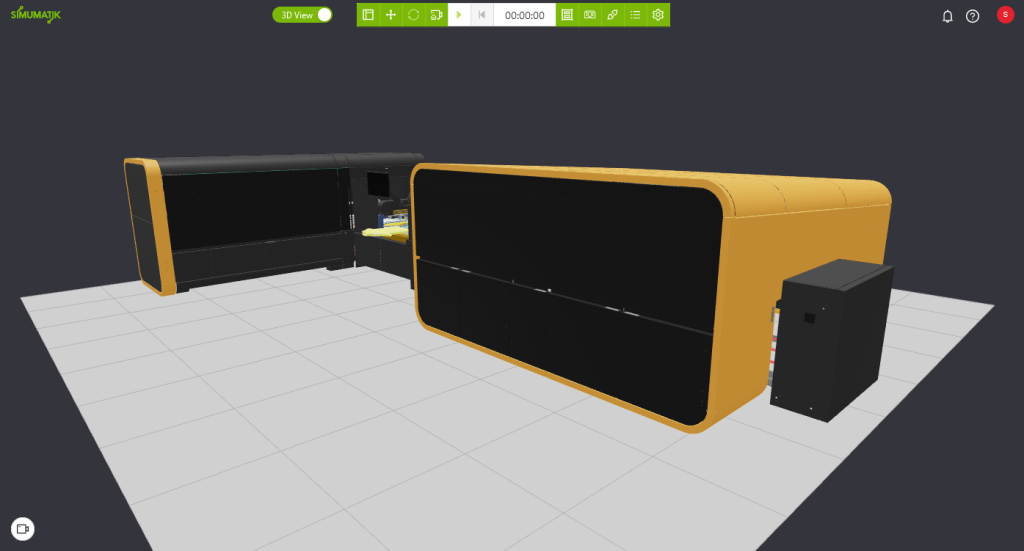
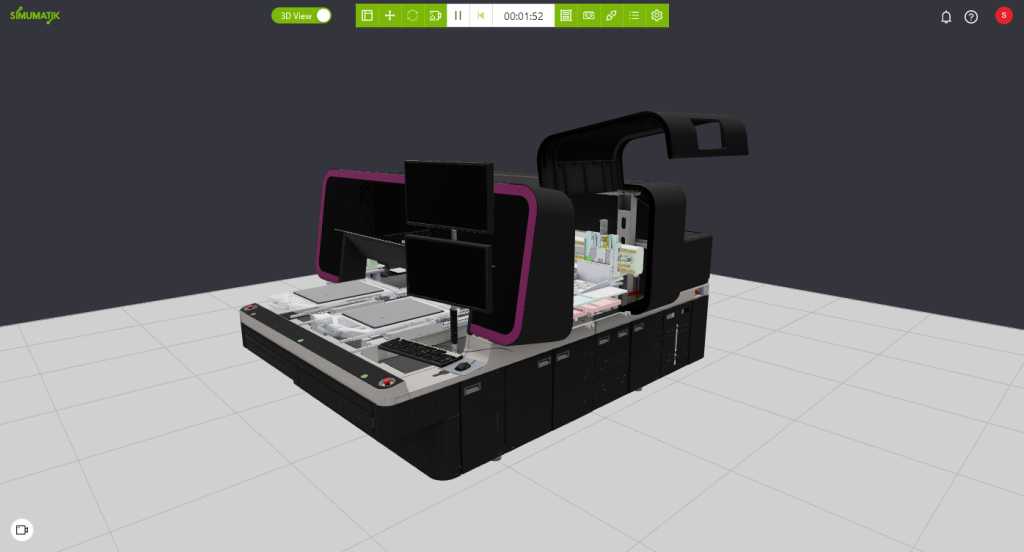